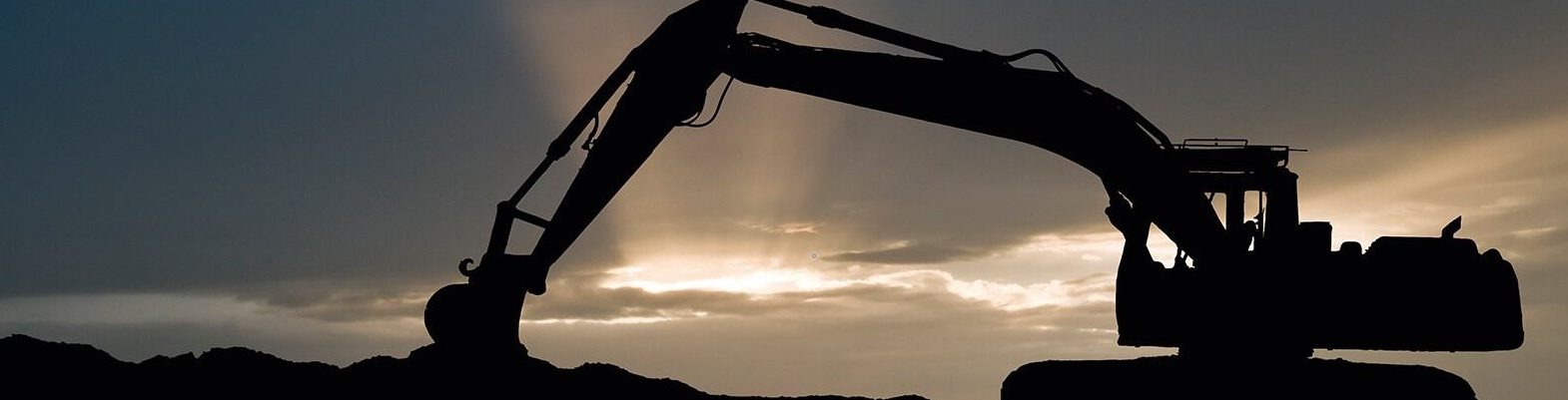
Lube-Spec’s Publications
Below are articles by Lube-Spec Ltd published in the Quarry Management magazine.
Aggregate Industries receive dose of preventative maintenance.
June 2008
A recently refurbished locomotive (pictured below). Operated by Aggregate Industries, is reaping the benefits of a custom Centralised Lubrication System as part of the company’s preventative maintenance programme and improve health and safety.
Leicester-based Lube-Spec Ltd, specialists in Lubrication Systems, were contacted about specifying a solution and recommended the Beka-Max EP1 progressive system.
There are 48 lubrication points on the locomotive, and due to the location of some points, this posed a safety issue for the engineer, who would have to climb, crawl, and carry equipment in confined spaces for manual greasing. Manual lubrication also incurs cost and downtime and is often not reliable.
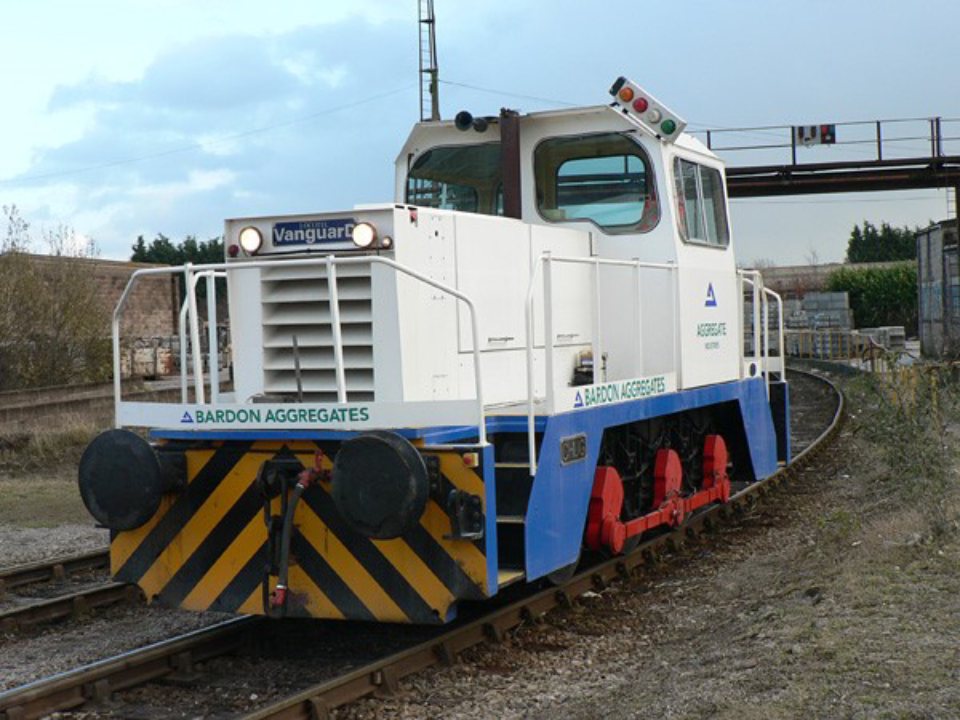
Company Director Mark Cherry said:
“Even with high-pressure pumping, it is difficult to get grease into a close-fitting bearing, as some surface areas will be in contact with each other under the weight of the machine. This often leads to a lack of effective protective lubricant between the bearings working surface area, which increases the risk of accelerated bearing wear.”
The Beka-Max EP1 Lubrication System feeds all the lubrication points on the loco and uses a special link arrangement connecting the wheel-rod bearings. This reduces the maintenance cost of replacing bearings through extended bearing life, minimises downtime by eliminating manual lubrication and, most importantly, improves the safety of operations on the engine. As a result, Aggregate Industries are now able to transport materials by rail more efficiently, thanks to increased running time of their locomotive.
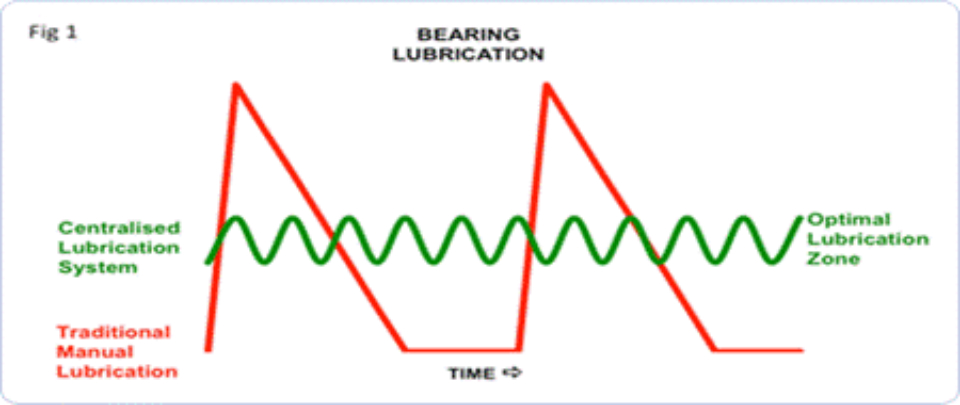
Bearing lubrication in the construction industry.
May 2016
Companies require reliability and value from their equipment, and therefore, getting the most from their bearings is key without incurring any unnecessary operating costs.
In a study conducted by a major component manufacturer, it found that over 60% of bearing failures were the result of inadequate lubrication and bearing contamination. The ramifications are, unsurprisingly, costly and can cause massive disruption to the production site.
Not only this, manual lubrication can be inconvenient; stopping a machine at regular intervals to lubricate bearings is expensive, increasing both downtime and reducing manpower. As a result, businesses will never be able to maximise the performance and value of their equipment.
Too much lubrication can potentially create a safety or environmental hazard, while too little lubrication causes bearing friction and wear. According to Lube-Spec, the use of centralised lubrication systems eliminates the ‘feast or famine’ conditions associated with manual lubrication.
A centralised lubrication system applies smaller amounts of lubricant frequently while the machine is in operation. This effectively keeps bearings in the Optimum Lubrication Zone (fig 1).
The key to unlocking the full value and potential of machinery
July 2020
Construction plant and machinery operates in some of the hardest and harshest conditions. With companies requiring reliability and value from their equipment, getting the most from their bearings without incurring any unnecessary operating costs is key. It is not only the heavy loads and rough working conditions that apply pressure on modern construction machines and equipment but also the users’ ever-increasing demand for performance and cost-efficiency.
In a study conducted by a major component manufacturer, it was found that more than 60% of bearing failures were the result of inadequate lubrication, bearing contamination and corrosion (see fig. 1). The ramifications of this are, not surprisingly, costly and can cause massive disruption to production. Fig.1
